Granite, a durable and versatile igneous rock, is widely used in construction, architecture, and landscaping. Its crushing and processing require advanced techniques and machinery to ensure high-quality output. This article explores the essential steps in granite processing and highlights innovative solutions that optimize efficiency and cost-effectiveness.
1. Primary Crushing: Breaking Down Large Granite Blocks
The initial stage involves reducing large granite boulders into smaller fragments. Mobile jaw crushers are commonly used for primary crushing due to their robustness and adaptability. These machines can handle hard, abrasive materials like granite with minimal downtime. For instance, the PE series jaw crushers (e.g., PE 250x400, PE 500x750) are designed for high-capacity primary crushing, ensuring uniform particle size and low wear rates .
2. Secondary Crushing: Shaping and Finishing
After primary crushing, secondary processes like impact crushing or cone crushing refine the material. Impact crushers excel in producing cubical-shaped aggregates ideal for construction projects, while cone crushers offer precise control over particle size distribution. The C106 jaw crusher and mobile cone crushing plants are popular choices for their durability and energy efficiency .
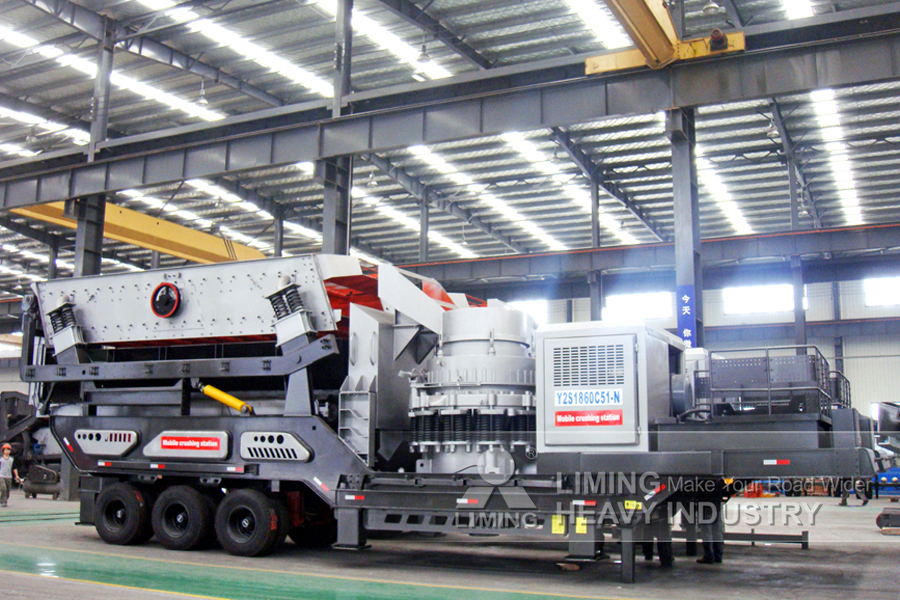
Cone mobile stone crusher
3. Advanced Processing: Sand Making and Recycling
Modern applications often require fine aggregates, such as silica sand. VSI (Vertical Shaft Impact) crushers and 5X series impact crushers are critical for sand-making processes. These machines not only crush granite but also shape particles to meet strict industry standards. For example, the 5X series from Liming Heavy Industry combines hydraulic systems and optimized rotor design to enhance throughput by 30% while reducing maintenance costs .
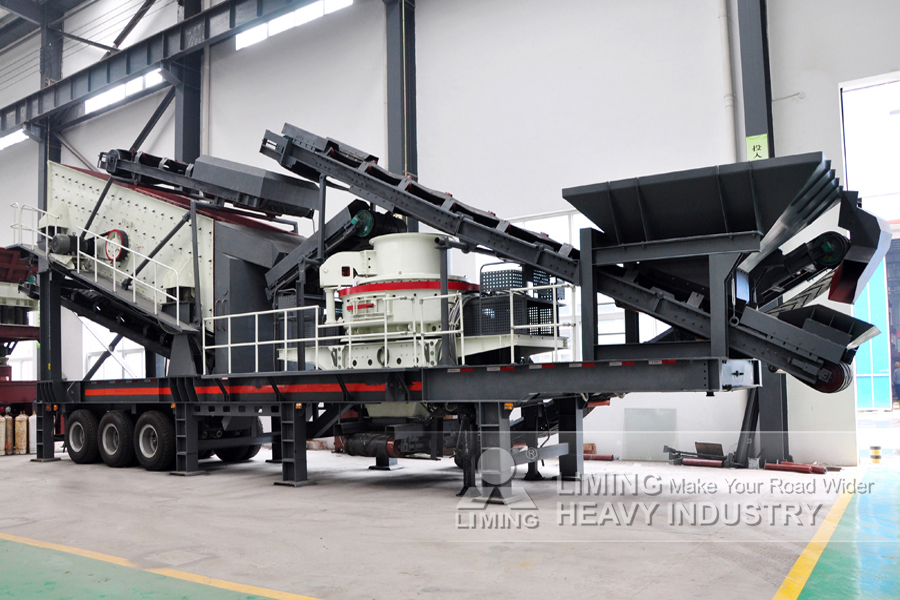
Mobile stone sand making machine
4. EPC Solutions for Turnkey Projects
For large-scale operations, Engineering, Procurement, and Construction (EPC) services streamline project execution. Companies like Liming Heavy Industry offer customized granite processing lines, integrating feeders, crushers, screens, and conveyors into a single system. Their modular designs allow easy expansion and adaptability to varying production needs, ensuring minimal downtime and maximum ROI .
5. Sustainability and Innovation
Emerging trends prioritize eco-friendly practices. Closed-circuit systems with dust suppression and wastewater recycling are now standard. Additionally, AI-driven automation optimizes machine performance, reducing energy consumption and labor costs.
Efficient granite crushing and processing hinge on selecting the right equipment and workflow. By leveraging advanced machinery like Liming’s 5X impact crushers and EPC solutions, businesses can achieve higher productivity, lower operational costs, and compliance with global quality standards. For tailored solutions, explore Liming Heavy Industry’s portfolio of granite processing equipment and turnkey projects .